In recent years, the government has been strongly supporting the development of the new energy vehicle industry, and the completeness and promotion of charging infrastructure corresponding to it are essential for the development of new energy vehicles. Since these charging stations are often placed outdoors, they require high resistance to oxidation and must be designed using sheet metal materials to achieve a long-lasting outdoor service life of up to ten years. Therefore, when designing our automotive charging station products, we chose a design that integrates both DC and AC charging capabilities. This design allows the product to provide fast charging for both DC and AC power sources.
View Introduction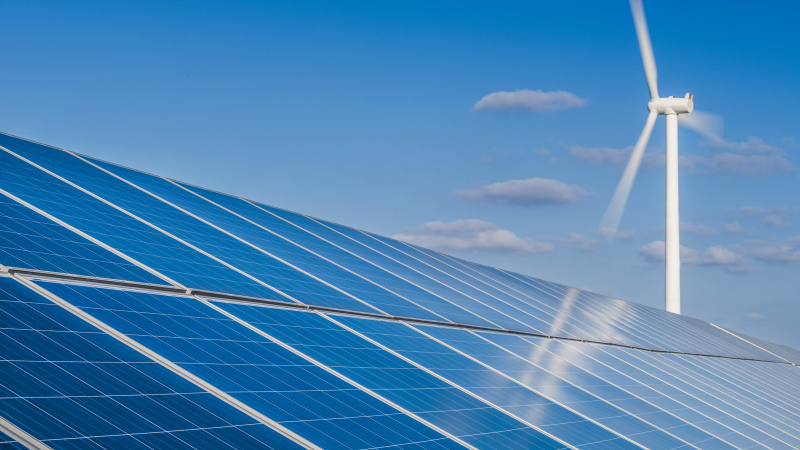
Solutions for New Energy Industry
The world is currently undergoing its third energy transition, moving from wood to charcoal, charcoal to oil and gas, and now transitioning from oil and gas to new energy sources. Currently, the three hottest sectors in the new energy industry are electric vehicles, energy storage, and clean environmental energy.
Charging Stations: In recent years, the government has been strongly supporting the development of the new energy vehicle industry. Correspondingly, the completeness and promotion of charging facilities are crucial for the development of new energy vehicles. Due to frequent outdoor exposure, these charging stations require high resistance to oxidation and must be designed using sheet metal materials to ensure they can withstand outdoor conditions for at least a decade. New Energy Vehicles: Employing lightweighting technology, as the core component of new-generation vehicles, the welding of lithium-ion power batteries involves multiple complex joints with high precision requirements. Traditional welding processes are no longer suitable for lithium-ion power battery manufacturing. Environmental Protection and Purification: Environmental machinery plays a significant role in domestic environmental investments, encompassing power equipment for conveying polluted fluid substances, such as pumps, fans, and conveyors, as well as complete sets of equipment including air purifiers, sewage treatment facilities, ozone generators, industrial oxygen generators, and more. However, the level of automation in these processes is relatively low.
- Charging Stations
- New Energy Vehicles
- Environmental Protection and Purification
Solution
Recommended machine model